Redefining the traditional farmhouse for the 21st century
Working with a package provider is a great way to start designing your timber frame self-build home, without the price tag associated with design fees. The case study below highlights what can be achieved working collaboratively with Fleming Homes’ architectural design team.
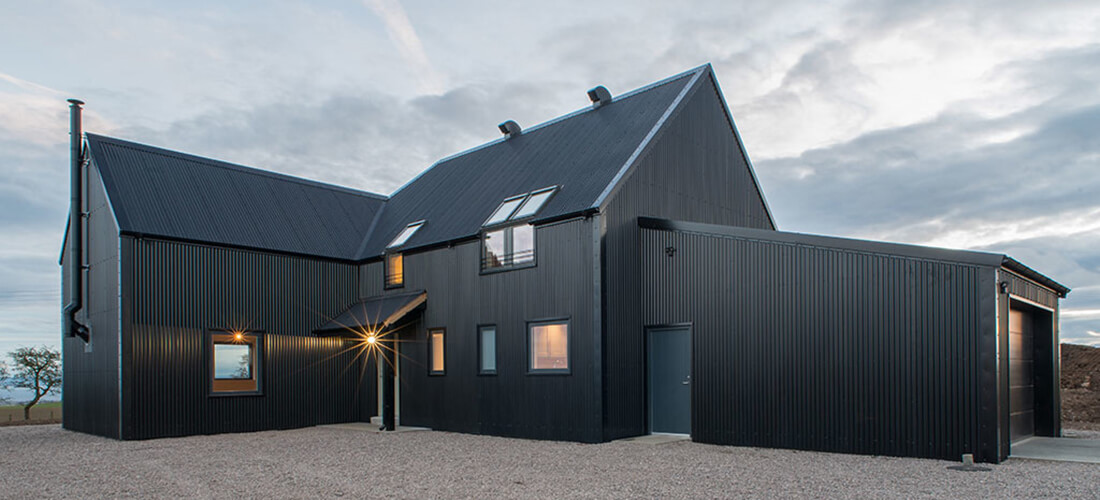
Struggling to attract or retain a head stock person forward-thinking employer, Balcaskie Estate, set out on an adventurous project to replace a 1970s bungalow which sat alongside a derelict farmhouse with an impressive contemporary self-build timber frame home. The design, choice of materials and quality of finish were all selected with the specific intention of helping to position farming as a great career choice.
Choosing to work with Fleming Homes’ in-house design service to realise their vision, the Balcaskie Estate team worked collaboratively with our architectural designers to translate their ideas into a design. Incorporating architecturally bold choices the aspiration was for the house to sit in harmony with the Estate’s portfolio of 56 traditionally built and listed farm properties. The finished house was clad with standard profile corrugated steel with a black painted steel finish. Internally, the four-bed farmhouse includes a big kitchen and office downstairs.
On completion of the initial designs, excited by the prospect of what could be achieved with timber frame, the Balcaskie team took the daring decision to go bigger and go higher. The initial designs were revised to create a house with more generous proportions; the design decisions representing an added investment in the prospective new occupier. Crucially, timber frame’s limitless design options enabled harmonisation of the priorities of the Estate and those of the family who would eventually reside there.
Once the design work was finalised and approved, Balcaskie Estate chose to use Fleming Homes’ architectural design team to achieve planning permission. Remarkably, despite some of the bold design choices, it sailed through the local authority’s planning process. This sign-off on the design and materials was an important milestone as it set a precedent with the local authority for future projects elsewhere on the Estate. On confirmation of full planning consent and then subsequent approval of the building warrant (again with help from Fleming Homes) the project moved through to Fleming Homes’ construction design team and offsite manufacturing facility to produce the hand-made timber frame.
The aspiration was to be as energy efficient as possible. With an investment in people again at the fore, it was important to the team leading the project that the house would be as cheap to run as possible for the stock person. Timber frame enabled a core layer of insulation to be housed within the structure itself ensuring a high-performing, thermally efficient home. Sound deadening insulation was also paramount (and easily integrated into the timber frame) to protect against the expansion and contraction of the steel roof and the consequent creaking.
Combining timber frame with a range of renewable technologies, the Balcaskie team were aiming for an environmentally friendly home. A ground source heat pump was chosen to ensure heating is available when needed and a 50kw solar array on a nearby farm building eliminates the need for oil and powers the house including an electric AGA. While the steel cladding may sit at odds with the house’s environmental credentials, steel does have an important role to play in agricultural sheds and so it serves as an important architectural feature that ensures the house is in keeping with the local vernacular.
The finished property is a spectacular family home that redefines the traditional farmhouse for the 21st Century. It challenges perceptions of what it means to live in tied accommodation and pushes the envelope when it comes to an agricultural career. We loved working on a project that put people first and prioritised high-quality, environmentally friendly housing stock as a key component in recruiting talent. The result is a stunning, highly specified house constructed within average build times and for a realistic self-build budget. Perhaps most importantly, it achieved the aim of attracting a talented stock person and their family to Balcaskie Estate.
“We’re very proud of the house. It works brilliantly as a farmhouse and it’s been an excellent exercise in testing what is possible in a greenfield site. It’s now a proven concept to help demonstrate how rural housing can fit within the landscape and help maintain a vibrant rural population” said Sam Parsons, Estate Manager, who went on to add “Working with Fleming Homes was an absolute pleasure. I’ve renovated 35 houses and 40 commercial buildings, and never have I had such a straightforward build. That’s no reflection on trades we have used elsewhere; it’s just there’s is no comparison with a timber frame new build”.